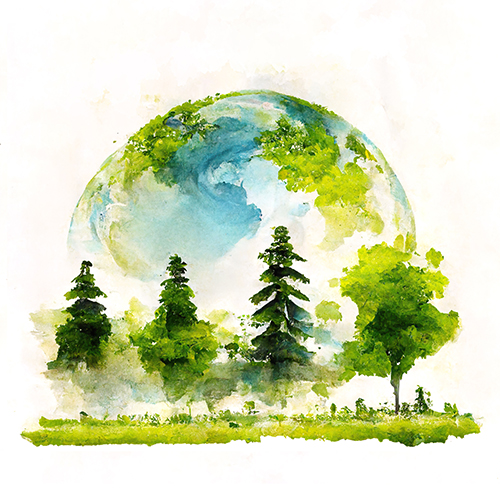
We specialize in water-based painting. The company is ISO 14001 certified.
Departments
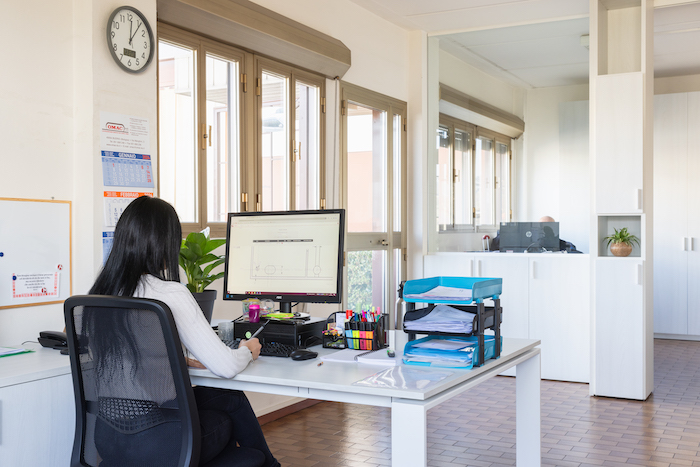
Administration and Logistics
Two people are responsible for administrative management, environmental management (ISO 14001), and logistics (Processing documents, Shipping, and updating price lists).
Production
Each phase of the production cycle is carried out with the utmost care and quality to achieve a final result free from any defects.
At the end of the cycle, tests are conducted on the resistance and thickness of the paint using micrometers.
Tecnovernici is equipped with a high-tech, environmentally friendly painting system, controlled by PLCs dedicated to the movement and management of all phases of the process (washing, booths, drying ovens).
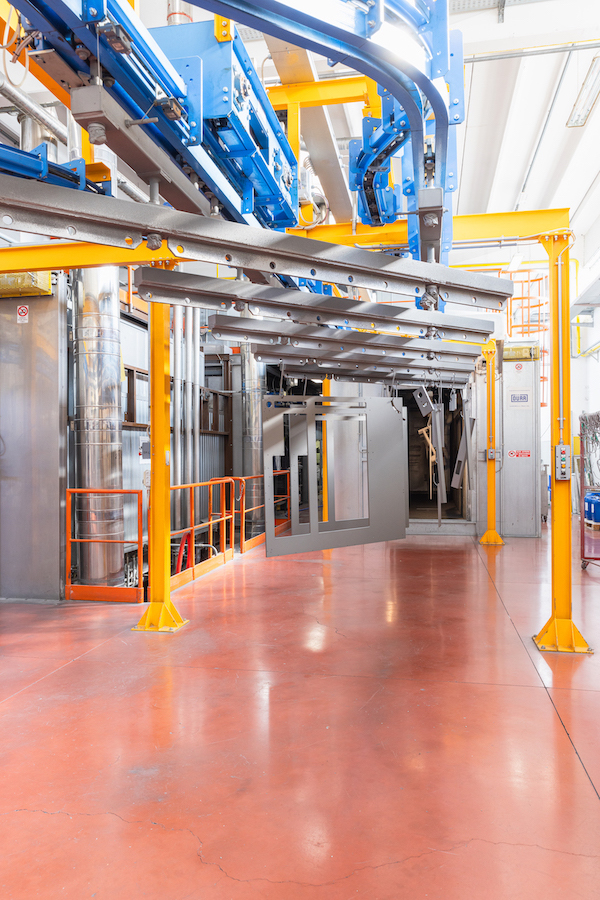
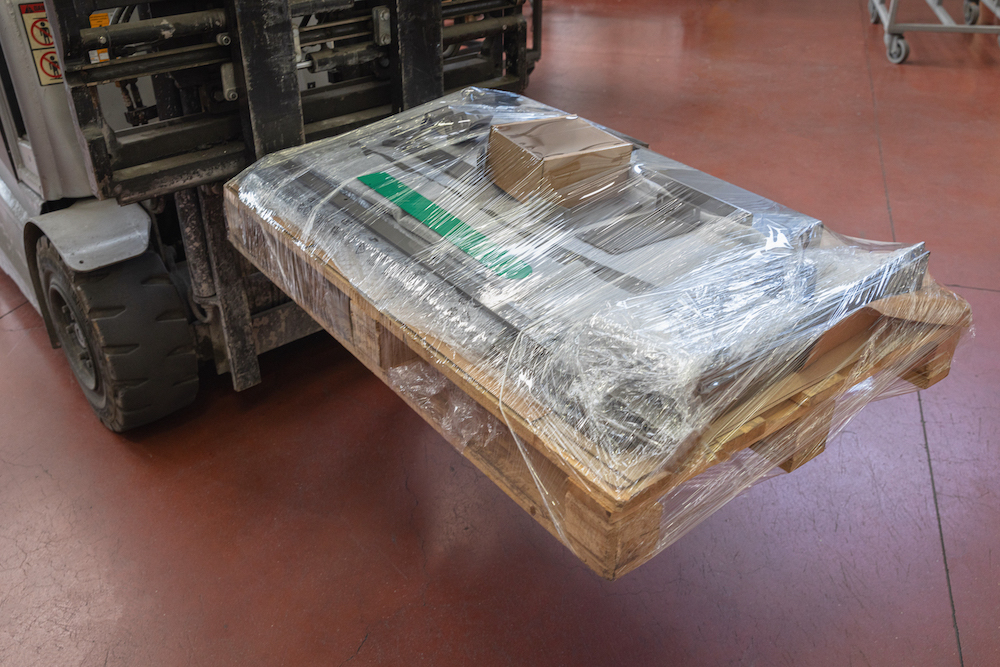
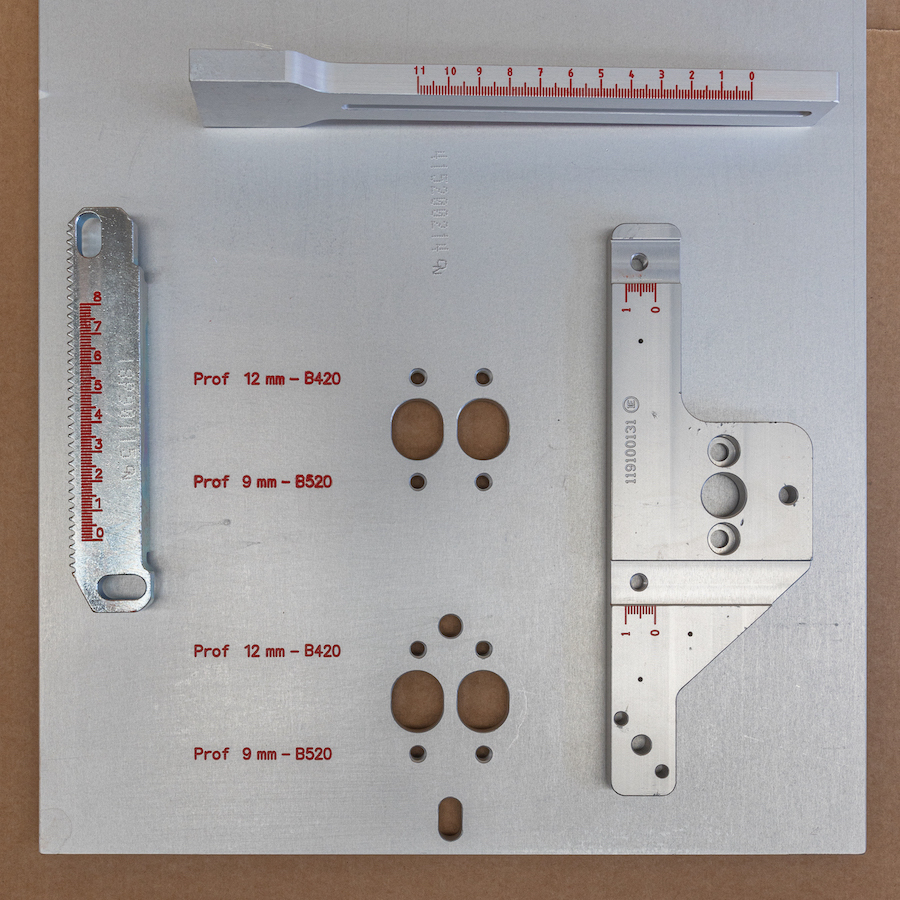
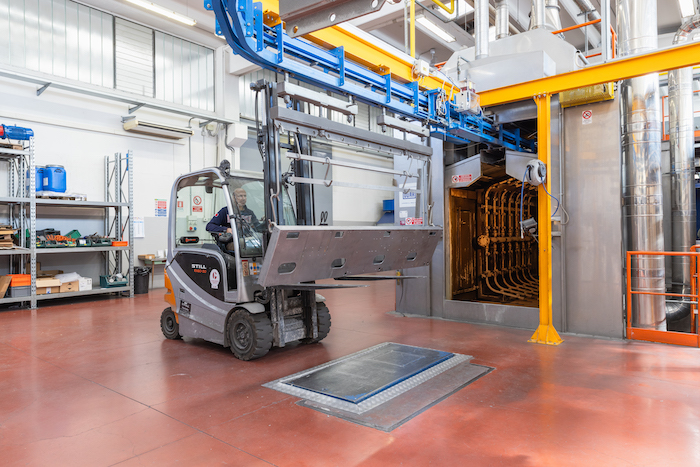
Produzione
Ogni fase del ciclo di lavorazione viene eseguita con la massima cura e qualità, per ottenere un risultato finale esente da qualsiasi difetto.
A fine ciclo vengono eseguiti controlli sulla resistenza e sullo spessore della vernice tramite micrometri.
La Tecnovernici è dotata di un impianto di verniciatura ad alta tecnologia e basso impatto ambientale, controllato da PLC dedicati alla movimentazione e alla gestione di tutte le fasi del processo (lavaggio, cabine, forni di asciugatura)
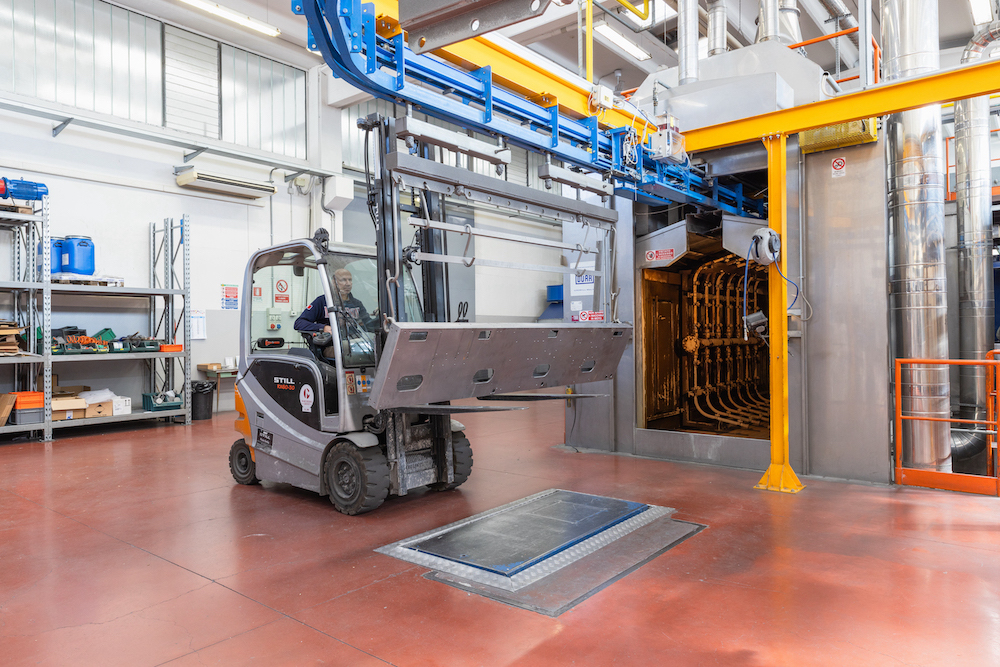
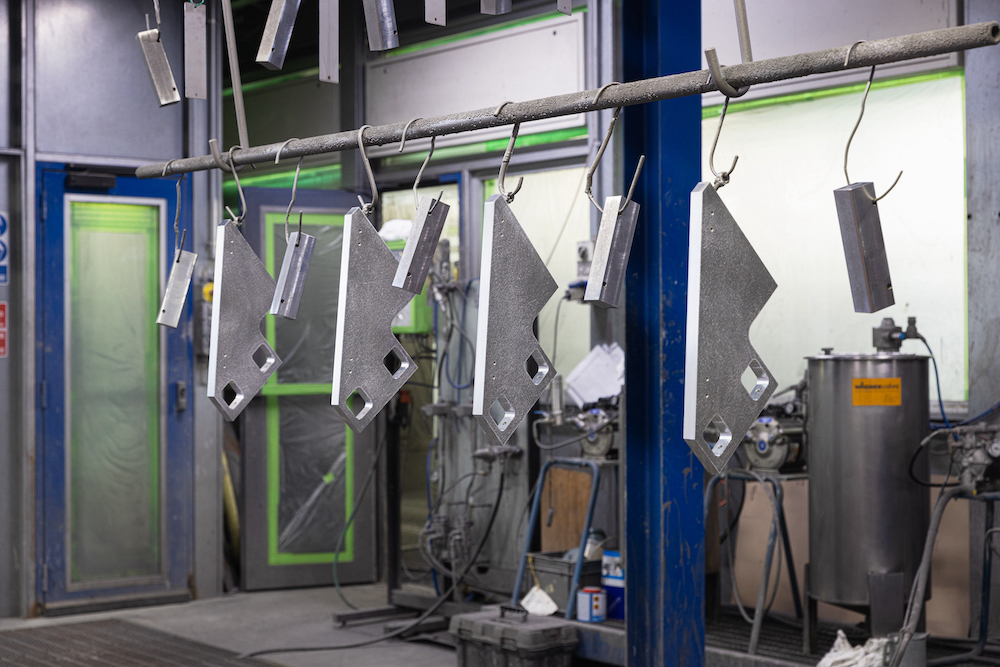
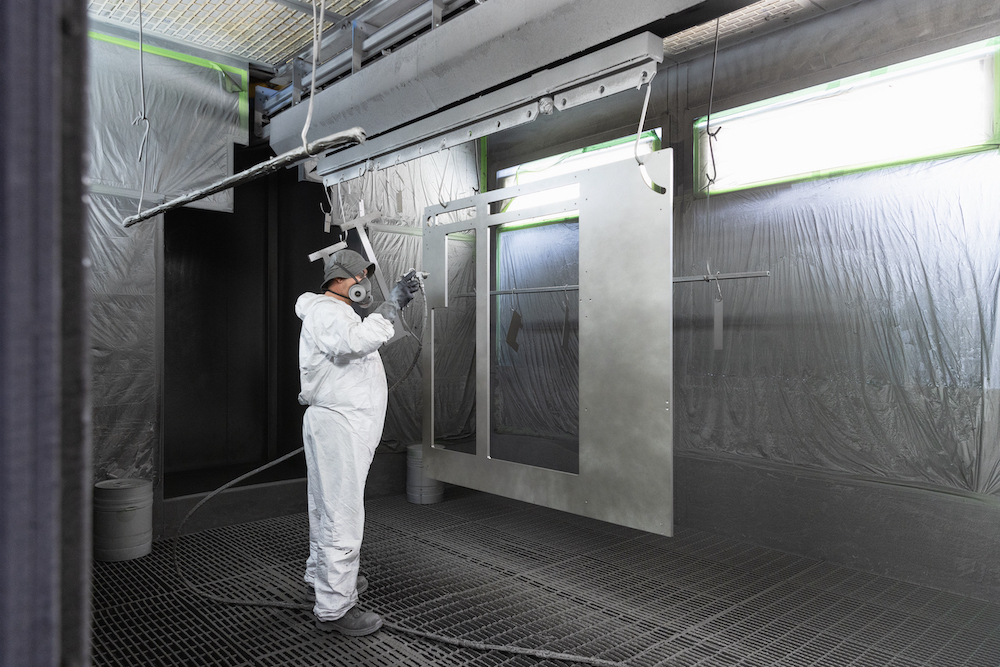
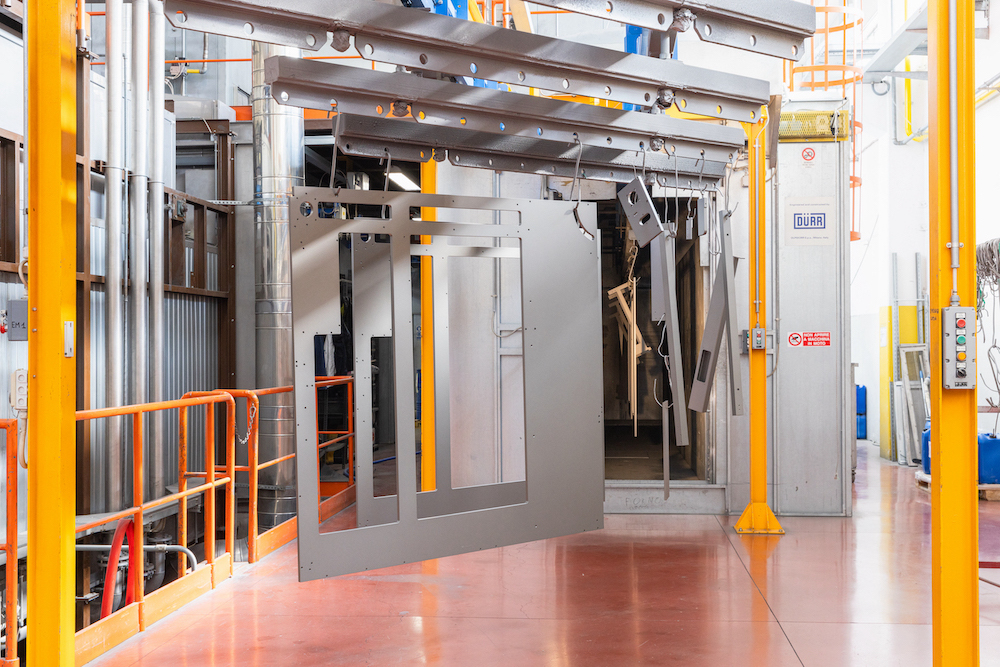
Chain Processing
Suitable for small to medium-sized parts. The items to be processed are hung on a special hanger and transported along the line with an overhead rail conveyor.
Preparation
Where possible, many parts are treated with surface sanding, using different grit sizes depending on the material, before being subjected to washing.
Washing
The parts enter a static tunnel where they undergo spray treatments, including phospho-degreasing at 60°C, followed by two rinses—one with cold water and the final rinse with hot water at 60°C. Afterward, the parts are dried with hot air jets up to 80°C in a special forced convection oven.
Finishing
After drying, the parts undergo filling, masking (and sanding where necessary), and a further light surface cleaning (if needed). These operations take place in a grated area with dust and vapor extraction.
Primer Painting
The application of the primer (base coat) takes place inside a specialized pressurized and heated booth, where treated air is introduced from above and extracted from below. The booth is equipped with a wet overspray removal system. After painting, the primer is leveled and dried in a heated tunnel at 50-60°C to optimize the subsequent application of paint.
Enamel Painting
The application of the enamel (paint) in a double coat is carried out inside a specialized pressurized and heated booth, where treated air is introduced from above and extracted from below. The booth is equipped with a wet overspray removal system. After painting, the enamel is leveled and dried in a heated tunnel at 50-60°C to optimize the paint drying phase.
Drying
The final stage of the painting process involves drying the paint in a specialized oven at 70-80°C. This final drying phase takes about 45-60 minutes. Afterward, the parts are left to cool in natural air.
Packaging
After cooling, the painted parts are removed from the hangers and placed on pallets, wrapped in cardboard and bubble wrap to protect the finish from scratches and impacts during transport. They are secured with plastic film or strapping where necessary.
Static Plant Processing
Suitable for large parts; if dimensions and weight allow, the items to be processed can be hung on a special hanger and transported along the line with an overhead rail conveyor, limited to the washing and preparation phases. If the dimensions and weight make this impractical, the preparation and washing phases are carried out manually on dedicated structures using specific products, in an area equipped with dust and vapor extraction.
Preparation
Where possible, many parts are treated with surface sanding, using different grit sizes depending on the material, before being subjected to washing.
Washing
Where dimensions and weight permit, a washing tunnel is used with phospho-degreasing at 60°C, followed by two rinses with cold water and hot water at 60°C, and subsequent drying in a specialized oven at 80°C with forced air. When this is not feasible due to the size or shape of the parts, cleaning is done manually in a designated area equipped with dust and vapor extraction, using degreasing and cleaning agents, and drying in air.
Finishing
The parts undergo filling, masking (and sanding where necessary), and a further light surface cleaning (if needed) within a grated area equipped with dust and vapor extraction.
Base Coat Painting
At the end of the preparation, large parts are transferred to the static, pressurized, and heated painting/drying booth, where the primer painting and drying phases occur. The booth is equipped with a dry filter overspray removal system.
Enamel Painting
After the primer has dried, the double layer of enamel is applied in the same pressurized and heated booth.
Drying
Within the same painting booth, the paint is dried at 65-70°C, completing the final drying process in approximately 45-60 minutes. Afterward, the parts are left to cool in natural air.
Packaging
After cooling, the painted parts are placed on pallets and packaged with cardboard and bubble wrap to protect the finish from scratches and impacts during transport. They are secured with plastic film or strapping where necessary.